Voestalpine works on hydrogen plasma for green steel production
Hydrogen plasma is used to reduce iron ore and smelt it into crude steel.
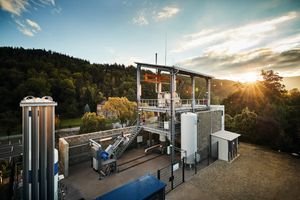
At the new pilot facility, which commenced operation in Donawitz in 2021, Voestalpine is researching the use of hydrogen plasma for the carbon-free manufacture of crude steel in a single process step.
As part of the “sustainable steelmaking” (SuSteel) research project, the company will investigate the use of hydrogen plasma in a carbon-neutral steel production process in a new pilot facility at the Voestalpine site in Donawitz. Voestalpine is currently the world’s only steel manufacturer conducting research into the use of hydrogen plasma in steelmaking.
Conventional steel production uses coke, coal, or natural gas as a reducing agent for ores. The SuSteel project replaces these with hydrogen. Hydrogen plasma is used to simultaneously reduce iron ore and smelt it into crude steel in a special direct current electric arc furnace. The advantage of using green electricity and hydrogen as the reducing agent is that water vapour is the only end product, completely avoiding carbon dioxide emissions.
Project partners joining Voestalpine in this basic research project include the K1-MET competence centre for metallurgy and the Montanuniversität Leoben. SuSteel is a COMET project, initially funded by K1-MET via the Austrian Research Promotion Agency (FFG) until 2023.
Voestalpine is consistently following its plan to achieve climate-neutral steel production. The aim is to partially replace the existing blast furnace route with hybrid steel production using electricity as of 2027 and to successively increase the share of green hydrogen used in the steel production process to 2050. “The requirements for realizing this revolutionary vision are clear: green electricity and hydrogen must be available in sufficient quantities and at prices which reflect market conditions,” Eibensteiner adds.
The Voestalpine works premises in Donawitz were deliberately chosen as the site for the new pilot facility. Here at the Group’s site in Styria, the Voestalpine Metal Engineering Division will produce high-grade steels for processing into special rails for railway infrastructure, premium wires for the automotive industry, and high-quality seamless tubes for oil & gas exploration.
Recent investments at the Donawitz site include the TechMet, a metallurgy technical research centre for the production of high-performance steels and the world’s most advanced and fully digital continuous casting line. The site also benefits from its proximity to the Montanuniversität Leoben; as part of the SuSteel project, this was the site of the first laboratory used to make steel by smelting around 100 grams of iron ore. The findings have now been used in the Voestalpine pilot facility, which can smelt around 90 kilos of ore.