Toshiba technology to cut iridium usage in electrolysis
PEM uses iridium, one of the rarest of all traded precious metals, as the catalyst in its electrodes.
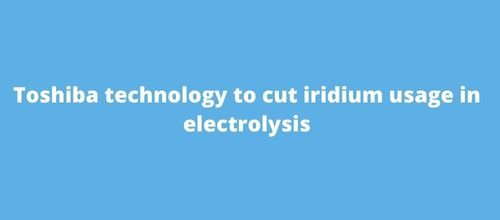
Toshiba Corporation has developed a large-scale production technology for the electrodes that realize high-level efficiency in Power to Gas (P2G) technology, essential know-how for advancing toward a carbon-neutral society while reducing the use of iridium to 1/10.
P2G uses water electrolysis to convert renewable energy into hydrogen for storage and transportation to where it is needed. Polymer Electrolyte Membrane (PEM) electrolysis is seen as a highly promising conversion method, as it reacts rapidly to power fluctuations and is highly durable.
Toshiba developed an iridium oxide nanosheet laminated catalyst that reduced the iridium requirement to 1/10 in 2017. The company has now developed large-scale production technology that deposits the catalyst over a maximum area of 5m2 at one time. This advance is expected to drive forward the early commercialization of P2G for large-scale power conversion and contribute to the realization of carbon neutrality. Toshiba is aiming for commercialization in FY2023 or after.
PEM uses a membrane electrode assembly (MEA) that integrates the electrolyte membrane and electrode. Large-scale hydrogen conversion of electricity requires a large number of MEAs.
However, the MEA electrode relies on a large amount of iridium to ensure sufficient electrolytic efficiency. Iridium is one of the rarest precious metals. The practical application requires reducing the iridium used, a real challenge.
Forming electrodes requires a uniform coating of fine iridium oxide particles, but reducing the iridium oxide results in uneven application and non-uniform reactions that degrade water electrolysis performance.
Using Toshiba’s laminated nanosheet structure in the catalyst layer successfully reduces the required iridium to 1/10, while maintaining the water electrolysis performance. It also significantly expands the deposition surface area. As sputtering is conducted in a vacuum, deposition on a large area is difficult.
However, by modifying the deposition distribution ratio for multiple metal targets, including iridium, and the oxygen input level, Toshiba has successfully developed a large-scale production technology that realizes catalyst deposition on an area of up to 5m2 at a time.
In collaboration with Toshiba Energy Systems & Solutions Corporation, Toshiba has built MEA prototypes with electrodes based on the developed technology and has begun evaluation testing with a water electrolyzer manufacturer. Going forward, the company will improve the yield and quality toward mass production of MEA, aiming for commercialization in 2023 or after.