Tenneco adds hydrogen to alternative fuels engine-testing capabilities
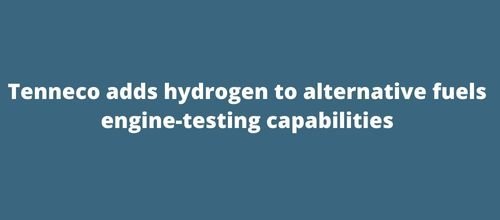
Tenneco has established new test facilities for hydrogen-powered internal combustion engines at its Powertrain test centers in Burscheid, Germany, and Ann Arbor, Michigan.
These two test cells specifically dedicated to hydrogen ICEs enhance the company’s globally integrated ICE test capabilities, supporting original equipment (OE) engine and vehicle manufacturers as they decarbonize the ICE. By adding H2-engine testing, Tenneco is well-positioned to provide technology solutions that can help to accelerate the reduction of carbon emissions of future combustion engine generations to achieve global climate goals faster.
“We support a pragmatic approach of complementary technologies that provide solutions for different transportation sectors,” said Stefan Rittmann, Vice President, Engineering with Tenneco’s Powertrain business group. “We contend it’s not combustion-engine technology causing green-house gas emissions in the product-use phase; it is the fuel used in the ICE that defines the vehicle emissions. Therefore, green hydrogen, which is produced from renewable energies and carbon-free by nature, offers great potential for cleaner transportation, especially in sectors difficult to electrify, such as heavy-duty commercial vehicles, on- and off-highway applications, and the industrial and marine sectors.”
As a leading supplier of engine components – including pistons, piston rings, bearings, seals and gaskets, valves, valve seats and guides, and ignition devices – Tenneco leverages its comprehensive ICE expertise in various hydrogen and alternative-fuel project partnerships with engine and vehicle manufacturers. Tenneco’s new test cells support manufacturers in their H2 ICE concepts, testing prototype engines and components for durability, wear, emissions, fuel-efficiency and performance.
“Using our knowledge about the influence of hydrogen on the combustion process and on the Powertrain Control Unit (PCU), we are able to address hydrogen-specific challenges like pre-ignition and H2-slip into the crankcase as well as the influence on tribology and materials,” said Dr. Steffen Hoppe, Powertrain’s Director Technology Rings & Liners, Tenneco. “The R&D from our H2 test benches, along with support from our simulation tools like PRiME3D®, can accelerate the development process and help our customers go to market with highly efficient H2 combustion engines faster.”
“Tenneco is dedicated to being a good corporate citizen; you see it in our operations and in our products,” added Troy Kantola, Powertrain’s Engineering Director, Technical Services. “Our efforts to enhance our test sites reflect this in that now we are equipped to serve our customers’ aspirations to reduce or eliminate entirely fuel-related CO2 emissions as quickly as possible.”