Paul Wurth, Saarstahl and Dillinger strengthen cooperation on H2Syngas
The cooperation agreement will help Paul Wurth to test the dry reforming process under industrial-like conditions, supporting the development of the new technology.
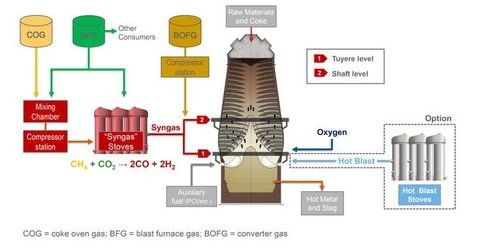
Paul Wurth (a part of SMS Group) has joined the H2Syngas project, a joint project of Saarstahl and Dillinger, to develop a technology using process gases and significant quantities of hydrogen in the blast furnace process, H2 Bulletin reports.
The first phase of the project will see building a pilot plant to test the dry reforming process on a small scale, which is scheduled to start operating this summer. The Luxembourg Ministry of Economy has awarded Paul Wurth a grant for the pilot project. A further objective of the pilot plant is to test materials and components regarding their suitability for the construction of an industrial-scale plant, which is vital for the selection of refractory materials used in the regenerative heat exchanger.
In the next stage, the process will be further developed to semi-industrial and later to industrial scale with support from public funding by producing larger amounts of hot syngas and inject them at shaft level in one of the two blast furnaces in Dillingen. Elaboration of a blast furnace shaft injection technology is thus part of the dry reforming development. The technology will enable steelmakers to reduce further their carbon emissions which is a step toward carbon-neutral steelmaking.
H2Syngas is a part of the cross-border hydrogen project in the Saar region. As part of the project, both steel companies will continue to work with Paul Wurth to develop the technology of using their own process gases for a blast furnace of ROGESA Roheisengesellschaft Saar mbH, a subsidiary of Dillinger and Saarstahl.
Dr Karl-Ulrich Köhler, Chairman of the Board of Management of Dillinger and Saarstahl, said, “By using hydrogen, we can further improve and nearly double the potential reduction of carbon. The creation of adequate energy infrastructure is a precondition for this.”
Paul Wurth develops the technology which is called the dry reforming process. Saarstahl and Dillinger will cooperate with Paul Wurth to further develop the technology of dry reforming of coke oven gas with blast furnace gas.
The technology enables the gas produced in the coke oven to be converted into a hot reduction gas, or syngas. This gas is enriched with hydrogen and then used as a reducing agent to reduce iron ores. Injecting the hot reducing gas into the blast furnace results in coke consumption and thus reduces carbon emissions. The use of process gases for metallurgical purposes can cut carbon emissions by around 12%.
Greens steel has become a major trend in the steel industry. In a separate development, today, UniCredit and DZ Bank have granted Duferco a loan of €72 million to construct a new production plant. SMS Group will provide the technology for the long steel plant at the San Zeno Naviglio site, Brescia. The plant will use energy from renewable sources, with the possibility of a hydrogen power supply.
H2 Bulletin covers dozens of hydrogen-related stories daily, which can be accessed through its H2 Intelligence platform.