MTU Aero Engines advances technological development of the FFC for zero emission aviation
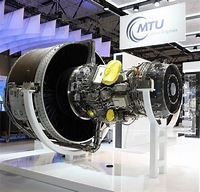
Zero emissions are the major goal of commercial aviation as well as the vision of MTU Aero Engines. With its Flying Fuel Cell™ (FFC), Germany’s leading engine manufacturer is steadily advancing the complete electrification of the powertrain, leaping from one milestone to the next.
A test campaign of the tank system was completed at MT Aerospace, while in Munich test cells are being built for the revolutionary drive technology in the Flying Fuel Cell, which will be further developed as part of the HEROPS EU research project.
“With a reduction of up to 95 per cent, the FFC takes the climate impact to almost zero,” explains Dr Stefan Weber. The reason: flying fuel cells do not emit CO2, nitrogen oxide (NOx) or particles – they only emit water. The principle: a flying fuel cell transforms hydrogen into electrical energy and achieves a high level of efficiency. Using this electrical energy, an electric motor drives the propeller. This highly efficient motor is developed by eMoSys GmbH, a Starnberg-based electric motor developer and small-volume manufacturer that has been part of the MTU network since last April. MTU’s FFC will initially be used on shorter routes in the shuttle and regional flight sector. Weber: “Here we are aiming for market launch starting in 2035.”
Together with MT Aerospace, MTU is developing a complete liquid hydrogen aircraft fuel system for commercial aviation that consists of tanks, sensors, heat exchangers, valves, safety systems, and regulators. The first system has now been tested at MT Aerospace in Augsburg – with great success. The comprehensive campaign demonstrated the effectiveness of the liquid hydrogen tank and supply system in various operating scenarios. “Verifying the most important operating modes is a breakthrough for hydrogen aviation technology,” comments MTU FFC Chief Engineer Barnaby Law.
A lot is going on at MTU in Munich, too: two FFC test cells are being built on the plant premises. The first is a fuel-cell-stack test cell that includes a hydrogen infrastructure, along with cooling water and compressed air supply. It is designed for stacks with an electrical output of up to 500 kilowatts per stack and will start operation in 2025. The second test cell is designed for the entire drive system.
Mid-January marked the start of the new HEROPS (Hydrogen-Electric Zero Emission Propulsion System) Clean Aviation research program. The goal – building on MTU’s FFC – is to develop technologies for a climate-neutral, hydrogen-powered electric powertrain that will power regional aeroplanes starting in 2035. Led by MTU, the seven partners first plan to analyze powertrain systems with an output of up to 1.8 megawatts, and then build a HEROPS ground demonstrator. This will demonstrate the feasibility of the groundbreaking new technologies and show that they can be scaled up to outputs between two and four megawatts, based on a modular drive architecture. The HEROPS industry partners are MT Aerospace, RTX’s Collins Aerospace, Lufthansa Technik, and Eaton, and the research partners are the Royal Netherlands Aerospace Center (NLR) and the Vienna University of Technology.