Haldor Topsoe to build SOEC electrolyser manufacturing facility
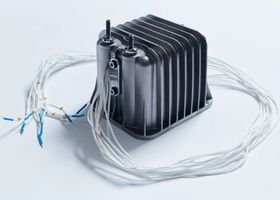
Haldor Topsoe, a Danish catalysis company, plans to develop a new manufacturing facility producing solid oxide electrolysers (SOEC). The initial capacity would be 500 MW/year with a plan to ramp up to 5 GW annually. The company is aiming to start the construction next year, with the operation is set for 2023.
“We have not decided on the location yet for the new SOEC [production facility] as a lot of parameters like the speed of construction, costs, logistics, workforce, legislation etc. are being evaluated right now,” Haldor Topsoe told H2Bulletin.
“Topsoe electrolysers, based on high-temperature SOEC, are up to 30% more effective than other technologies like PEM and alkaline. Therefore, our customers need fewer units to produce the same amount of green hydrogen,” the company explains.
The company further added that it is an emerging market, and we are confident that the production costs per kg of hydrogen will be industry-leading. Production of green hydrogen is influenced by a multitude of factors such as project size, integration and especially the cost of electricity for the individual projects.
Roeland Baan, CEO of Haldor Topsoe, said, “Topsoe already has a number of technologies and several others under development that will ensure that the company will play a leading role in the energy transition, reducing carbon emissions worldwide.”
The company also offers the technology for producing blue hydrogen, a route for making hydrogen from natural-gas-based with carbon capture option. It is also engaged in projects producing green hydrogen, green ammonia and biofuel. Some of the projects include the Helios project in Neom, DeLille project, green Copenhagen, green ammonia facility in Esbjerg and green methanol facilities in Scandinavia.
The SOEC is built of abundant and low-cost ceramic materials. It is composed of anode, cathode and electrolyte. It makes hydrogen and oxide ions at the cathode by water molecules where oxide ions are then pass through the electrolyte to the anode to become oxygen. The water-splitting process requires a 700C temperature. CO2 can also be electrolysed in the SOEC, where the CO2 is reduced to CO with O2 as a byproduct.