Cement producers explore hydrogen to tackle emission
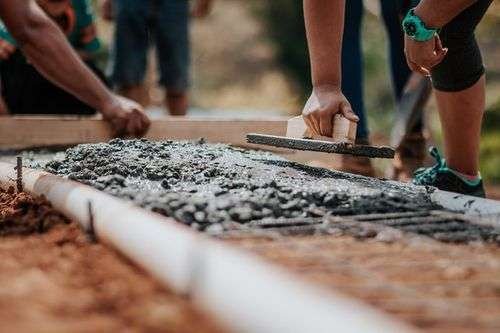
Cement is one of the most polluting industries in the world and has been facing significant challenges in its efforts to achieve carbon neutrality. A substantial amount of CO2 is released during the production of cement and its substrate- cement clinker. Limestone, which is the main ingredient for producing cement is the chief culprit behind the emission.
Causes of emissions
Nearly half of all emissions from cement production is direct emission and caused by a process called calcination- a process when limestone is heated and break down into calcium oxide and CO2. Fossil fuels such as oil, coal or natural gas are burned to heat the kiln. Therefore, combustion of these fuels emits additional CO2, which is around 40% of the total emission from the production. This part of the emission is categorised as indirect emission. Similarly, other parts in the plant also need electricity for operations, which make up the remaining 10% share. Indirect emission can be reduced by switching to biofuel or renewable. However, cement producers can do very little when it comes to direct emission by using conventional methods.
Hydrogen is becoming a part of the solution
Two main approaches can be used to help reduce direct emission. One way is to substitute or mix limestone with alternative materials such as coal fly ash and blast furnace slag. However, it has a limit and can cause other issues. The second option is to capture the CO2 through carbon capture and storage (CCS), which is a complex process and requires a substantial investment.
Employing the CCS approach to dump CO2 underground is probably not a sensible long term approach. CCS can become a profitable and sustainable part of a circular economy if the CO2 is recycled, and that is where the ‘utilisation’ part comes into the equation. The process is known as carbon capture, utilisation and storage (CCUS), which is also referred to as carbon capture, utilisation and sequestration. CCUS is now getting more traction especially pairing with hydrogen to produce high-value chemicals.
How are some cement producers using hydrogen in pilot projects?
Carmeuse
Carmeuse which is a Belgian lime and limestone producer with operations in Africa, Europe and North America spearheaded into producing e-methane (methanation) on an industrial scale by combining green hydrogen with the concentrated CO2 from the lime kiln in Wallonia Belgium. The CO2 will be concentrated from a new type of lime kiln while hydrogen will be produced through a 75 MW green hydrogen electrolyser production plant. E-methane will be supplied to industrial and transport sectors to help them in decarbonisation. The project implementation will start in 2022 and is expected to be in operation by 2025.
Carmeuse has said to take the full responsibility for developing the lime kiln. It has partnered with John Cockerill, a Belgian engineering company and Engei, a French energy transition specialist. John Cockerill will develop the 75 MW electrolyser plant at an Engie site at Charleroi, whereas Engie will take the ownership and operation responsibility of the electrolyser plant, producing green hydrogen. Storengy, which is an affiliate of Engie, will oversee the building and operation of the methanation process. The project is estimated to cost € 150 million (US$ 179 million) and the partners already applied for EU Innovation Fund and Important Project of Common European Interest (IPCEI).
Cemex
In March 2020, Cemex, a Mexican multinational building materials company, announced its long-term plan to 2030, aiming to reduce its CO2 emission by 35% from 1990 level to 520kg CO2/t of cementitious product. Among other changes, the company also considered hydrogen injection as a part of fuel source, as it allows for higher alternative fuel substitution and reduces heat consumption.
Hanson Cement (HeidelbergCement)
Hanson Cement, a subsidiary of Germany-based HeidelbergCement, is conducting a study using biomass and hydrogen fuels aiming to run cement and lime kilns with a zero-carbon fuel mix. The £6.2 million project is expected to be completed in March 2021, is funded by the Department for Business, Energy and Industrial Strategy (BEIS). The project follows a BEIS-funded feasibility study in 2019, which determined that CO2 emission can be eliminated during the cement-making process by using a combination of 70% biomass, 20% hydrogen and 10% plasma energy.
The project aims to test that theory to see whether a combination of hydrogen and plasma technology can be used to make cement production carbon neutral. Hanson Cement uses its Ribblesdale cement works in Lancashire, UK for the trials, which uses hydrogen and biomass fuels in the cement kiln. It is estimated that it could save 2 million tonnes of CO2 annually if implemented across the UK cement industry.
LafargeHolcim
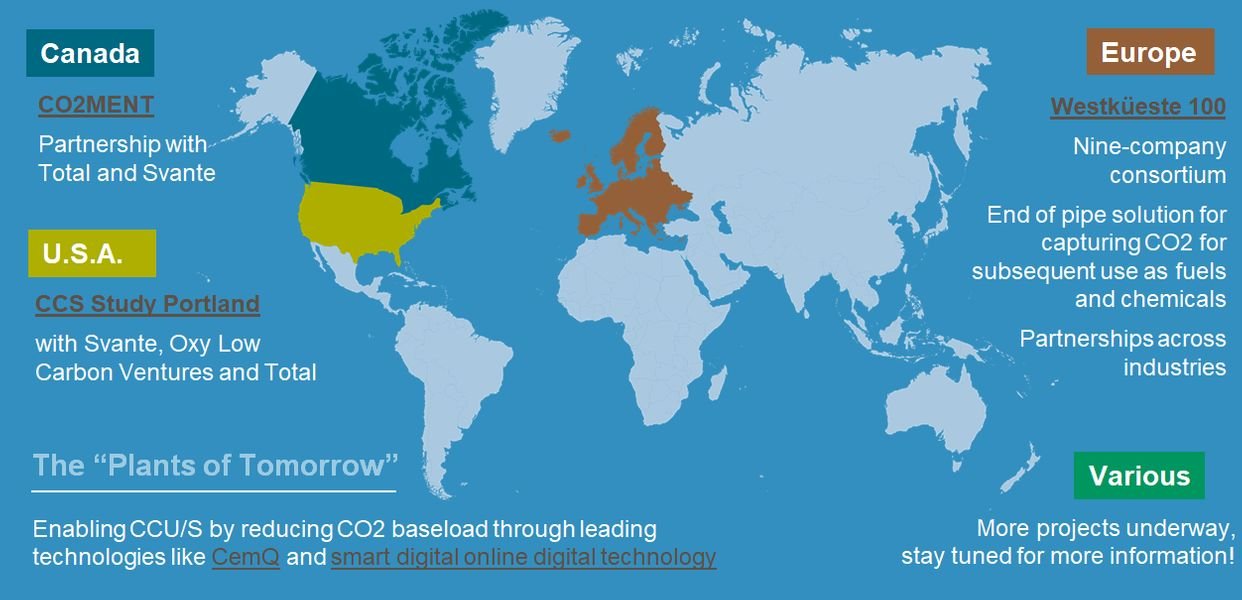
LafargeHolcim is the largest cement producer outside China with 270 sites globally. Its CCUS portfolio consists of over 20 projects across Europe, Canada and the US. Below are some of the selected projects, where we can see that some of them are carbon storage rather utilisation projects.
In Austria, Lafarge Zementwerke will build a CCSU at its Mannersdorf cement plant by 2030. The project is called ‘Carbon2ProductAustria’ (C2PAT), capturing all the 0.7 million tonnes/year CO2 for processing into synthetic fuels, plastics or other chemicals. Lafarge is joined by three Austrian partners: OMV, a producer of oil and gas, Verbund, an electricity provider, Borealis, a chemical producer. Verbund will produce hydrogen; OMV will transform the captured CO2 into olefins, fuels and plastics; Borealis will use some of OMV’s products as a feedstock to make plastics.
In Spain, LafargeHolcim is working on a pilot plant for carbon capture, aiming to turn the CO2 into agricultural use. In Germany, Holcim Deutschland is part of Westküste100 (the consortium of ten companies), planning to turn CO2 captured at the Holcim’s Lägerdorf cement plant into synthetic fuel using hydrogen. This project will have a capacity of 1 million tonnes/year of CO2. In the first phase, a 30 MW electrolyser will be built to produce green hydrogen using offshore wind energy. Initially, the cement plant will be converted to an oxyfuel combustion process.
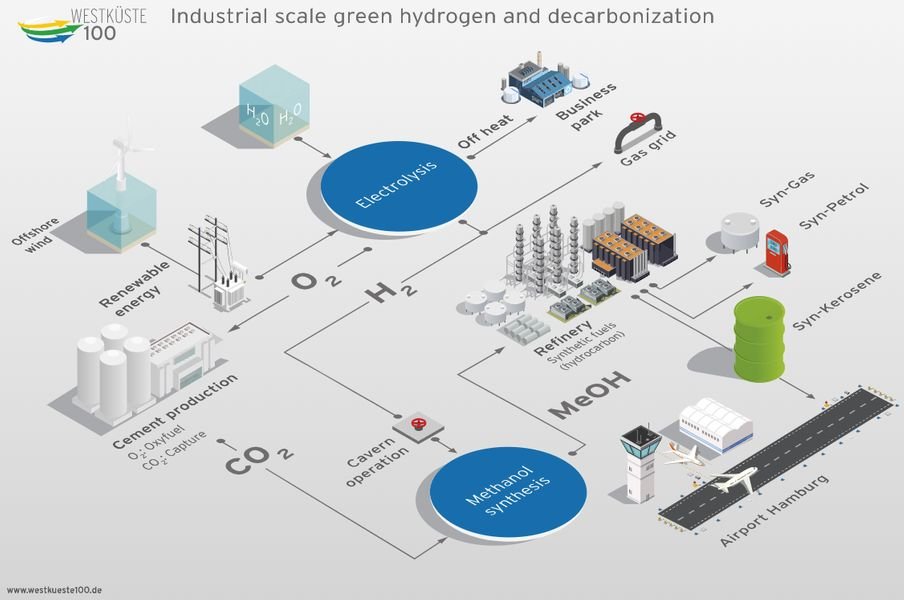
Photo: Westküste100
In the US, LafargeHolcim’s is working on a joint study of a carbon-capture facility at the Holcim Portland Cement Plant in Colorado to sequester CO2 underground permanently, meaning no utilisation of carbon. In Canada, LafargeHolcim has established a consortium of partners that include Svante Inc, Oxy Low Carbon Ventures LLC and Total to study the commercial viability of the carbon capture facility. It assesses the feasibility of 2 million tonnes of CO2 per year at LafargeHolcim Richmond cement plant.