ArcelorMittal plans big for decarbonising steelmaking
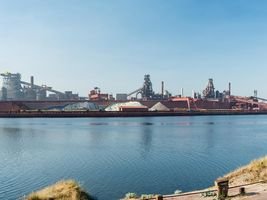
ArcelorMittal and Air Liquide have partnered to produce low-carbon steel in Dunkirk, France, using low-carbon hydrogen combined with CO2 capture technologies, H2Bulletin reports.
Both companies agreed to decarbonise the Dunkirk industrial basin as pressure is mounting on the hard-to-abate industries such as the steel industry to accelerate the decarbonisation process. The plan is to build a production plant on its Dunkirk site combining direct reduced iron (DRI) unit and a submerged arc furnace (SAF) to produce steel with less emission.
The project will cut its carbon emission in its Dunkirk steel making operations by 2.85 million tonnes/year by 2030. ArcelorMittal has set a goal to reduce its carbon emission in the European operations by 30% by 2030 before achieving carbon neutrality by 2050.
To DRI process runs on natural gas and eliminates the need for coal to make iron. With the emergence of hydrogen as a decarbonisation tool, steelmakers have been rushing for the direct reduction of iron technologies. Air Liquide will supply low-carbon hydrogen as well as implement CO2 capture technologies in Dunkirk.
ArcelorMittal Dunkerque operates one coke oven and two sinter plants to feed three blast furnaces for producing slab used to make flat steel. However, it is unknown what would happen to the steelmaking facilities if the DRI and SAF project materialises.
Both partners have also jointly applied for funding under the Important Project of Common European Interest (IPCEI) scheme for hydrogen.
In a separate development, today (17th March), ArcelorMittal launched its XCarb™ sustainability initiative to work towards carbon-neutral steel.
XCarb aim is to bring all the company efforts towards carbon-neutral steel under one umbrella with three initiatives. The first one is to issue green steel certificates to help steel buyers reduce their Scope 3 emissions. ArcelorMittal expects to produce 600k tonnes of equivalent green steel to be available by the end of 2022. Green steel certificates are issued based on its efforts incorporating CO2 saving by using various approaches such as Torero (transforming biomass into bio-coal for the use in the blast furnace) and Carbalyst (capturing and converting blast furnace waste gas into bio-ethanol for producing low-carbon chemical products) to capture hydrogen-rich waste gases during the steel production process and reusing it in the blast furnace.
The second initiative is the ‘recycled and renewably produced’, which means steel produced through Electric Arc Furnace (‘EAF’) route using scrap steel. Through this steelmaking process, the carbon footprint can be reduced substantially to 300kg of CO2/tonne, which is normally 1.85 tonne of CO2 per one steel tonne. The origin of power used in steelmaking would also be independently verified.
As a part XCarb, the third initiative is the ‘innovation fund’, which would invest about US$ 100 million annually in companies developing zero carbon steelmaking technologies that can be commercially scalable and have a great potential to decarbonise the steelmaking process.