Schaeffler develops hydrogen mobility for commercial vehicles
Schaeffler sees fuel cells as an important part of the overall mix of drive technologies for commercial vehicles.
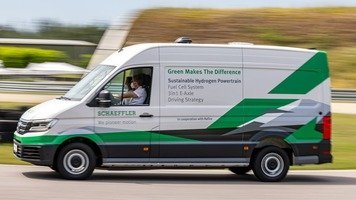
Schaeffler is developing innovative components for fuel cell systems and laying the groundwork for them to be produced on an industrial scale.
It will present a demonstration vehicle built from the ground up based on an electric van. The vehicle is driven by a Schaeffler 3in1 e-axle powered by a fuel cell system made using Schaeffler components.
Schaeffler has been developing metallic bipolar plates since 2017 and is currently making them at a pilot plant at its Herzogenaurach location. The process of manufacturing bipolar plates draws on the company’s extensive expertise in multiple manufacturing processes, including cold forming, stamping, joining, and surface treatment.
Schaeffler is also leveraging its bearings know-how to develop various axial and radial air foil bearings for fuel cell air supply, nozzles for hydrogen recirculation, and key components for the coolant management system, including a thermal management module and smart valves for decentralized coolant regulation. In addition, the company is continually growing its expertise and capabilities in fuel cell system control, including software modules for fuel cell-specific functions.
The vehicle will be unveiled to the public for the first time at the IAA Transportation show (booth U47 on the open-air site). It features a 13 kWh battery with a maximum power output of 85 kW, and a fuel cell system rated for a continuous output of 50 kW. The propulsion is provided by a Schaeffler 3in1 e-axle, complete with power electronics, with a maximum output of 140 kW. Schaeffler uses the vehicle as a development platform for testing and optimizing the interaction between the various system components.
Schaeffler set up a pilot production plant at the start of 2022. The plant is designed in such a way that it can be used to manufacture bipolar plates in sizes ranging up to the larger 1,800 by 600 mm formats used in electrolyzers.
The individual process steps performed by the pilot plant, designed in partnership with Schaeffler’s in-house Special Machinery unit, are already fully automated. The pilot plant is part of a new hydrogen centre of excellence at the company’s Herzogenaurach location, which includes a large testbed for testing electrolyzer and fuel cell technologies at the component, stack, and complete system levels.
Matthias Zink, CEO of Automotive Technologies at Schaeffler AG, said, “Initially, fuel cell drives will be used mainly in long-haul commercial vehicles. Vans will benefit from this technology too because they regularly also cover longer distances.”
Dr Jochen Schröder, head of Schaeffler’s E-Mobility business division, said, “We are using our high-precision forming and stamping technology and innovative surface coating processes to make ultra-efficient, high-performance bipolar plates.”