Hybrit technology is set for industrial commercialisation in Gallivare
SSAB, LKAB and Vattenfall will use hydrogen to make fossil-free iron by 2026.
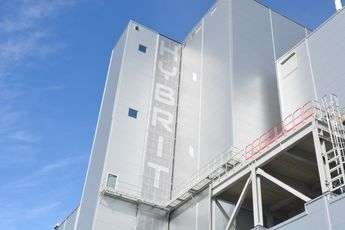
Hybrit technology will see its first industrial application in Gällivare, northern Sweden, where technology developers plan to build the world first fossil-free sponge iron plant, H2Bulletin reports.
SSAB (A major Swedish steelmaker), LKAB (Europe’s largest iron ore producer) and Vattenfall (a major European energy company) started developing Hybrit technology in 2016 by setting up a company called Hybrit Development AB. The technology aim is to produce fossil-free steel by replacing coking coal with fossil-free electricity and hydrogen.
Industrialisation is intended to start with the first demonstration plant, which will be ready in 2026 for the production of 1.3 million tonnes/year of fossil-free sponge iron in Gällivare. The demonstration plant will be integrated with an iron pellet making plant. The goal is to expand sponge iron production to a full industrial scale of 2.7 million tonnes by 2030 to supply SSAB, among others, with feedstock for fossil-free steel.
Sponge iron is commonly known as DRI (direct reduced iron) and is made from the direct reduction of iron ore (lumps, pellets, or fines) to iron. The process is conducted by using a reducing gas or elemental carbon produced from natural gas or coal. Due to the decarbonisation drive, hydrogen has been preferred over natural gas recently.
Gällivare is an ideal location for the sponge iron plant due to its proximity to LKAB’s mining production and processing, saving energy and transportation costs. Vattenfall ability to provide clean energy is another advantage.
Martin Lindqvist, President and CEO at SSAB, said, “We are seeing a clear increase in demand for fossil-free steel and it is right to speed up our groundbreaking cooperation.”
Jan Moström, LKAB President and CEO, said, “The whole process starts with top quality iron ore in the mine and our transition plan gives strong economies of scale that pave the way for the competitive production of fossil-free steel by our customers.”
In February this year, H2 Green Steel (H2GS), a Swedish consortium that Scania leads, plans to develop a 5 million tonnes/year steel plant in the Boden-Luleå, northern Sweden. The Hybrit technology inspired the project though it is unknown whether the Hybrit plant in Gällivare would supply any feedstock to H2GS.
Moreover, SSAB and LKAB will also look into developing a fossil-free steel value chain of iron ore mine-steel plant-customers, with Vattenfall providing electricity and hydrogen gas. SSAB will accelerate its plan of the Luleå pilot plant, which would see hydrogen produced through electrolysis, making sponge iron, through direct reduction of iron ore pellets. The technology is being tested using hydrogen in iron ore reduction at the pilot plant in Luleå, with SSAB expects prototype deliveries this year. The pilot plant for a direct reduction in Luleå was inaugurated in August 2020. There are also plans for an underground storage facility in the rock for fossil-free gas. SSAB also plans to convert its Oxelösund steel plant by 2025 and aims to start selling fossil-free steel by 2026.